United States Aluminum: Blast Mitigation Design Guide
Home
Blast Mitigation Systems
|
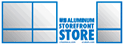 |
In the blink of an eye, the contemporary concept of facility security was forever changed on the morning
of April 19, 1995. The attack on the Oklahoma City Murrah Federal Building, and the implications of the
complex physical interactions caused by an event of that magnitude compelled Architects, Engineers and
the Federal Government to reexamine the design process and expectations for government facilities. A blast
event of that nature turns conventional glass into a multitude of tiny shards propelled at over 200 feet per
second into a structure. Studies estimate that over 60% of the casualties in the Murrah Building were glass
related. Reports of shattered glass were received from up to 14 blocks away from the Murrah Building,
demonstrating the vulnerability that structures near a possible target site face for collateral damage.
United States Aluminum has designed and tested the Defender Series of Blast Mitigation Glazing Systems, manufactured
to the highest standard, to provide protection for GSA, DoD and private sector facilities. These systems
cover the range of glazing requirements, including storefront, entrance, curtain wall and window systems
designed to meet a variety of protection levels. While our dedicated blast mitigation project management
team and application engineers will provide assistance in selecting the appropriate system for a project, it is
strongly recommended that each project design team work with an experienced blast consultant to ensure
compliance.
Blast Mitigation Design Guide
An emerging trend of the green building movement is the emphasis placed on daylighting in buildings. Daylighting is the design practice of placing windows, and sometimes reflective surfaces, so that during
the day natural light provides effective internal lighting. Design consideration must be given to glazing used
in buildings assessed to be at risk of explosions, both accidental and intentional. Buildings considered at
risk include GSA and DoD Federal buildings, Office buildings, research facilities and buildings in proximity to
possible target buildings.
As shown in this illustration, a blast wave is an extreme energy release manifested in 4 forms; light, sound, heat and a shock wave. The chronology of a blast wave consists of a instantaneous positive pressure
wave that quickly reaches
the peak overpressure point
measured in psi exerting positive
pressure on a glazing assembly
which decreases exponentially
in milliseconds to the zero
pressure point followed by a
negative pressure phase where
air rushes into the void behind the blast wave pulling the glazing
assembly and debris outward.
Blast mitigation glazing assemblies have three critical stress points; anchor, frame and laminated glass. Both monolithic and insulated blast mitigation glass units typically include a thin interlayer material, usually polyvinyl butyral (PVB), to bond annealed or tempered layers of
monolithic glass together. The glazed assembly must
have a secure anchoring system to keep the framing
in place, the framing system must keep the laminated
glass unit in place, and though the laminated glass unit
may fracture, the glass must remain adhered to the PVB
layer according to the Performance Condition of the project. The design purpose for these blast resistant
glazed units is to absorb energy and debris from a blast event by deforming in its framing, instead of being
rigid in an attempt to deflect the energy.
A host of government and non-government agencies have addressed the issue of blast mitigation for facilities. The United States federal Interagency Security Committee (ISC) developed a blast-resistance standard outlining criteria for design. The General Services Administration (GSA) implemented the ISC Security Design Criteria as its design standard. The GSA is responsible for nearly 60 agencies, the U.S. Courts and Congress; encompassing over 340 million square feet of space in office buildings, courthouses, border stations and
warehouses. The GSA guideline for glazing system performance, the GSA-TS01-2003, outlines approved
methods for shock tube testing, arena testing and test modeling with software.
This illustration shows a cross section of
a test structure defining the protection
levels correlated in table 1: ISC Security Design Criteria Blast Protection Levels for
Windows. Table 1 describes the six defined
ISC Protection Levels and the associated
glazing response expectations.
The GSA and the Department of Homeland
Security use a standard called the Federal
Security Risk Management (FSRM) as a
threat/vulnerability assessment and risk
analysis to determine the protection level
required for a facility.
The Department of Defense (DoD) developed a blast mitigation standard for use in designing DoD facilities,the Unified Facilities Criteria (UFC) – DoD Minimum Antiterrorism Standards for Buildings.
Table 2-1 Levels of Protection (New and Existing Buildings) and Table 2-2 Levels of Protection (Expeditionary and Temporary Structures) detail the varying levels of protection, the potential structural damage and potential injuries. Section B-3.1 Standard 10 Windows and Skylights of the DoD’s UFC 4-010-01 establishes design expectations for blast mitigation glazing systems in response to the designated Levels of Protection.
UFC 4-010-01 establishes a minimum standoff distance of 82 ft. from roadways and parking lots with certain
exemptions like post exchanges that may require different blast mitigation performances due to the proximity
of vehicular access.
Section B-3.1 of the UFC specifies that hardware, connectors, glazing stops and anchors be calculated to
a load of 10.8 psi for glazed units of 10.8 square feet or less, and 4.4 psi for glazed units of more than
10.8 square feet but less than 32 square feet.
Section 3.1.1.1 sets minimum glazing requirements as two 1/8” annealed glass panes bonded together
with a minimum of a .030” polyvinyl-butyral interlayer, as shown in Table B-2 and Table B-3. For insulating
glass units a minimum ¼” laminated glass is required for the inboard pane. These standards are based on
application of the ASTM F 2248 Standard Practice for Specifying an Equivalent 3-Second Duration Design
Loading for Blast Resistant Glazing Fabricated with Laminated Glass and the ASTM E 1300 Standard
Practice for Determining Load Resistance of Glass in Buildings.
|
|